Keynote Speaker I:
"Polarimetric Radar Cross-Section Measurement and Analysis of In-Flight UAVs at X- and L-Bands "
Abstract: A comparative first-order statistical analysis is presented for radar cross-section (RCS) data of in-flight unmanned aerial vehicles (UAVs) collected at the X- and L-bands. The study is based on measurements gathered with a frequency-modulated continuous-wave (FMCW) radar in a rural area during the simultaneous flight of a commercial and a professional-grade drone. The objective is to assess how the statistical behavior of the RCS depends on radar frequency, polarization configuration, and drone type. The analysis is based on the empirical cumulative distribution function (ECDF) of the normalized RCS data and its comparison with different theoretical models, whose goodness of fit of which is assessed via the Cramer-von Mises distance. In addition, dispersion metrics such as standard deviation, interquartile range and full range are calculated to provide a quantitative measure of the RCS variability under different operating conditions. The results show that, regardless of the frequency band, each UAV conforms to a distinct RCS fluctuation model. Moreover, for a given UAV, the best-fitting pattern changes depending on frequency and polarization. These variations reflect the different structural characteristics of the UAVs as well as the frequency/polarization RCS dependence due to the different response of the scatterers composing the drone.
Bio-Sketch
Antonio De Maio (S'01-A'02-M'03-SM'07-F'13) was born in Sorrento, Italy, on June 20, 1974. He received the Dr.Eng. degree (with honors) and the Ph.D. degree in information engineering, both from the University of Naples Federico II, Naples, Italy, in 1998 and 2002, respectively. Currently, he is a Professor with the University of Naples Federico II. His research interest lies in the field of statistical signal processing, with emphasis on radar detection and optimization theory applied to radar signal processing. Dr. De Maio is a Fellow member of IEEE and the recipient of the 2010 IEEE Fred Nathanson Memorial Award as the young (less than 40 years of age) AESS Radar Engineer 2010 whose performance is particularly noteworthy as evidenced by contributions to the radar art over a period of several years, with the following citation for "robust CFAR detection, knowledge-based radar signal processing, and waveform design and diversity". Dr. De Maio is the recipient of the 2024 IEEE AESS Warren White Award, to recognize a radar engineer for outstanding achievements due to a major technical advance (or series of advances) in the art of radar engineering, with the following citation “for contributions to radar signal processing techniques for target detection, waveform design and electronic protection”.
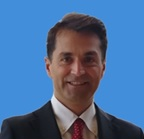
University "Federico II" of Napoli, Italy
Keynote Speaker II:
"Active Flow Control with a Co-Flow Jet in Improving the Performance of a Transonic-Truss Braced Wing
"
Abstract: The Transonic Truss Based Wing (TTBW) is a high aspect ratio wing that requires a truss to support its large span. The high wing design is beneficial since it allows for integration of efficient large diameter fans and open rotor propulsion systems such as the GE RISE engine concept. The TTBW was developed by NASA/Boeing to improve aircraft performance reaching a lift to drag ratio of ~26. This along with weight reduction in comparison to a cantilever wing reduces the fuel burn. Decades of airfoil design in both the military and commercial sectors has produced highly optimized airfoils for a range of flow regimes. Recent research has largely shifted towards the development of active-flow control (AFC) technology to further improve the airfoil performance. A variety of AFC techniques such as circulation-control airfoils, synthetic jets and plasma actuators have been shown to improve the maximum lift coefficient by delaying flow separation. In this presentation, AFC using a co-flow jet (CFJ) is applied to TTBW to further increase its L/D ratio and energy efficiency. CFJ is a zero-net mass flux active flow control technology that has been shown to improve the performance of supercritical airfoils at transonic conditions at lower angles of attack. A TTBW aircraft configuration is considered with 767 fuselage and Boeing SUGAR IV high aspect ratio wing planform of RAE 2822 supercritical airfoil section. CFJ is implemented at jet injection location at 3% from the airfoil leading-edge and jet suction location at 75% from the leading-edge. The jet momentum value is chosen so that there is no choking at the suction slot. Computations are performed on unstructured grids at Mach 0.8 and 0.745 for angles of attack ranging from one to five degrees using the CFD solver Ansys Fluent.The RAE 2822- TTBW without CFJ achieves a lift to drag ratio of 21.68 but with the addition of CFJ, this increases to 26.76.
Bio-Sketch
Prof. Ramesh Agarwal is the William Palm Professor of Engineering in the department of Mechanical Engineering and Materials Science at Washington University in St. Louis. From 1994 to 2001, he was the Bloomfield Distinguished Professor and Executive Director of the National Institute for Aviation Research at Wichita State University in Kansas. From 1978 to 1994, he was the Program Director and McDonnell Douglas Fellow at McDonnell Douglas Research Laboratories in St. Louis. Dr. Agarwal received PhD in Aeronautical Sciences from Stanford University in 1975, M.S. in Aeronautical Engineering from the University of Minnesota in 1969 and B.S. in Mechanical Engineering from Indian Institute of Technology, Kharagpur, India in 1968. Over a period of 50 years, Dr. Agarwal has worked in Computational Fluid Dynamics, Computational Acoustics and Electromagnetics, Computational Materials Science and Manufacturing, Nanotechnology and Nanomaterials, Multidisciplinary Design & Optimization, and their applications to problems in mechanical and aerospace engineering, and in energy and environment. He has made both fundamental and applied contributions to modeling, simulation and optimization of aerospace products, turbomachinery and pumps, chemical looping combustion (CLC), geological sequestration of carbon and wind turbines among others. His most recent work involves application of Machine Learning/Neural Networks to these disciplines to improve performance. He is the author and coauthor of four books on CLC, CCUS, Mixed-Flow Pumps and Multiphase Flows, and over 600 publications and has given many plenaries, keynote, and invited lectures at various national and international conferences worldwide in over sixty countries. He serves on many university (some international), government and industry advisory boards. He is a Fellow of 32 professional societies including American Institute of Aeronautics and Astronautics (AIAA), American Society of Mechanical Engineers (ASME), Institute of Electrical and Electronics Engineers (IEEE), Society of Automotive Engineers (SAE), American Association for Advancement of Science (AAAS), American Physical Society (APS), and U.K. Institute of Physics (IOP) among others. He has received many prestigious honors and national/international awards from various professional societies and organizations including the AIAA Reeds Aeronautics Award, SAE Medal of Honor, SAE Aerospace Innovation Award, ASME Fluids Machinery Design Award, ASME Honorary Fellowship, Royal Aeronautical Society Honorary Fellowship and European Academy of Sciences and Arts membership.
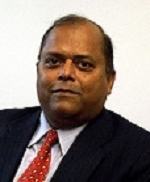
Washington University in St. Louis, USA
Keynote Speaker III:
"Thermal Management Systems for Electric Vehicles
"
Abstract: Energy management in electric vehicles is a complex, multivariable challenge. It requires a combination of model-based design, system identification, and careful consideration of trade-offs and constraints.
Among the various subsystems, the thermal management system (TMS) plays a critical role in maintaining optimal operating temperatures for key vehicle components, including the powertrain and the cabin.
Effective thermal management is essential not only for ensuring safety and reliability but also for maximizing efficiency and vehicle range—particularly in battery electric vehicles (BEVs), where thermal loads directly impact battery performance and longevity.
Decisions regarding control strategies, component sizing, and system topology (i.e., the layout and architecture of the thermal system) must be made early in the vehicle development process. These early-stage design choices are pivotal to ensuring that the TMS is capable of meeting performance requirements across a wide range of operating conditions.
As the automotive industry continues to shift toward electrification, the importance of robust and efficient thermal management systems becomes increasingly significant.
Bio-Sketch
Kambiz Ebrahimi is a Chartered Mechanical Engineer and Professor of Advanced Propulsion in the Department of Aeronautical and Automotive Engineering at Loughborough University, UK. He completed his PhD in dynamic and control at Cardiff University. Prior to joining Loughborough, he was Professor of Mechanical Engineering at the University of Bradford, where he also served as Director of the Hybrid Powertrain Engineering and Research Centre (HYPERC). His primary research interests lie in the dynamics, control, and condition monitoring of mechatronic systems. Dr Ebrahimi received the Ford Motor Company Award in 1999 for his pioneering work in web-based condition monitoring of engine transfer lines—an early application of digital twin technology for machine fault diagnosis using model-based prognosis. He has served as Principal Investigator on numerous industrially focused research projects, including: Validation Platform for Engine Calibration (Ford) Advanced Combustion Turbocharged Inline Variable Valvetrain Engine (Ford); Design and Prototyping of Power Generators for Remote Valve Actuation Turbocharger Blade Deflection Monitoring System using Tip Timing (Cummins Turbo Technologies), Data Acquisition and Processing for Rotating Shaft Telemetry Systems (ARAMCO). CO₂ Reduction through Emission Optimisation (Jaguar Land Rover). Since 2012, he has served as Chair and Organiser of the Powertrain Modelling and Control Conference.
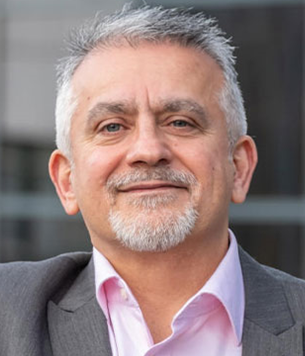
Loughborough University, UK
Keynote Speaker IV:
"Wearable Systems based on Mechanical Signals for Monitoring Cardiorespiratory Activity
"
Abstract: Wearable systems have been developed for a variety of use, including clinical care, wellness, occupational settings and sport science. Recently, the demand for advanced wearables capable of estimating cardiorespiratory parameters has extended across diverse domains, including aerospace. Indeed, in aerospace environments, cardiac and respiratory parameters, such as respiratory rate, heart rate, and heart rate variability, are key indicators of emotional stress, cognitive loading, fatigue, cardiac events, and respiratory distress. Monitoring these aspects can be beneficial for ensuring crew health, performance, and mission safety. This talk provides details on wearable systems for cardiorespiratory monitoring, with a special focus on those that are based on recording mechanical parameters generated by breathing and heartbeats. The talk will cover key design principles, materials used to develop the sensing elements, validation methods and the implementation of these systems in various use cases will be presented. Finally, an overview of the state-of-the-art algorithms for processing and extracting meaningful cardiorespiratory parameters from signals recorded by wearables will be presented.
Bio-Sketch
Emiliano Schena received his Bachelor, Master and PhD degree in Biomedical Engineering from University of Campus Bio-Medico of Rome (UCBM). He is now full professor in Mechanical Measurements and Sensors at the Department of Engineering at UCBM, Rector’s delegate for the research valorization and Campus Academy and Course Director of the “Biomedical Engineering Bachelor’s Degree Course”. He is research collaborator at the Fondazione Policlinico Campus Bio-Medico di Roma and Adjunct Professor at University of Arkansas (Rome Program). His main research interests include the design, development and assessment of wearable systems for monitoring physiological parameters, human motion and plant status. He was the recipient of many award and principal investigator/coordinator in number of industrial, national and European research projects and co-founder of Heremos s.r.l. He is the Treasures of the IEEE Italy Section, IEEE Senior Member, Counselor of the IEEE Student Branch of UCBM, and past chair of the Italy Chapter of the IEEE Sensors Council. He is author of more than 400 journal and referenced conference publications.
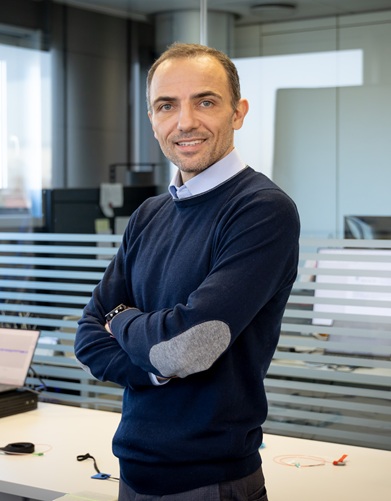
University Campus Bio-Medico of Rome, Italy